Mechanical seal test rig
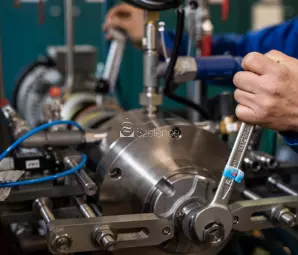
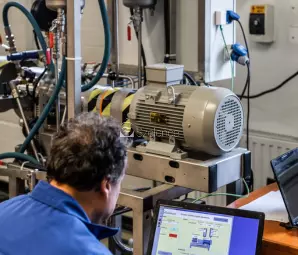
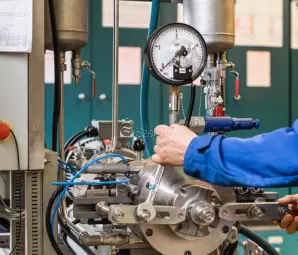
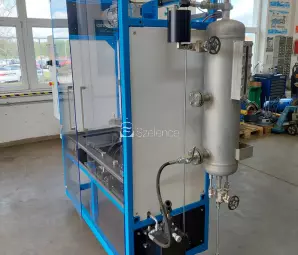
About dynamic testing
Szelence has a 30-year history and many decades’ worth of combined experience with mechanical seal repair. We found that in many cases to check a repaired seal with a simple static pressure test is not sufficient. Some faults may only show up while rotating or when the seal is close to its operating conditions.
Course of a typical mechanical seal test
- The tested seal is mounted on the test chamber with adapter plates and sleeves. Adapters ar available for ISO or API 610 standard dimensions.
- The mechanical seal test rig’s process and buffer/barrier reservoirs are filled with water or ethanol according to the test plan.
- Prescribed tests and cycles are performed. Everything is measured, controlled and logged by a PLC.
- During the mechanical seal testing operation, the leakage can be visually observed. Pressures, temperatures, VOC concentration and shaft power can be read off the HMI screen in real time.
- Following the test, a report is created by our engineer based on the collected data.
Our mechanical seal test rig’s features and advantages
- Successful seal repair is only 100% guaranteed by dynamic testing.
- No unnecessary downtime or delays to restart the pump or other rotating equipment.
- Any single or dual mechanical shaft seal can be mounted on the test rig with a shaft diameter between 35 and 100 mm
- 35 bar maximum working pressure. Most seals can be tested under close to real process conditions.
- Water or ethanol can be used as test liquids. The latter for measurement of gasous emmissions.
- A three-phase motor drives the tested seal at 2 or 4-pole speeds in any direction
- Up to 7.5 kW shaft power.
- PLC control with a HMI running on a Windows PC.